Hello everyone, I’m HUA (M2), and I’m thrilled to have had the opportunity to attend Interaction 2024, held at the Hitotsubashi Hall in Tokyo from March 6th to 8th, 2024. This event was an incredible chance for me to delve into cutting-edge research and design and to engage with students, educators, and professionals from various fields. The excitement of being part of such an inspiring and creative gathering was truly exhilarating.
During the three-day conference, I participated in various exciting lectures and interactive experiences with anticipation. I am particularly concerned about issues related to AI, VR,AR and sustainable design, as I believe these fields will be an development trend in the future. At the same time, I have focused on research related to gaze estimation and gaze tracking, not only because it is related to my own research, but more importantly, I hope to establish connections with like-minded people and find inspiration from their research.
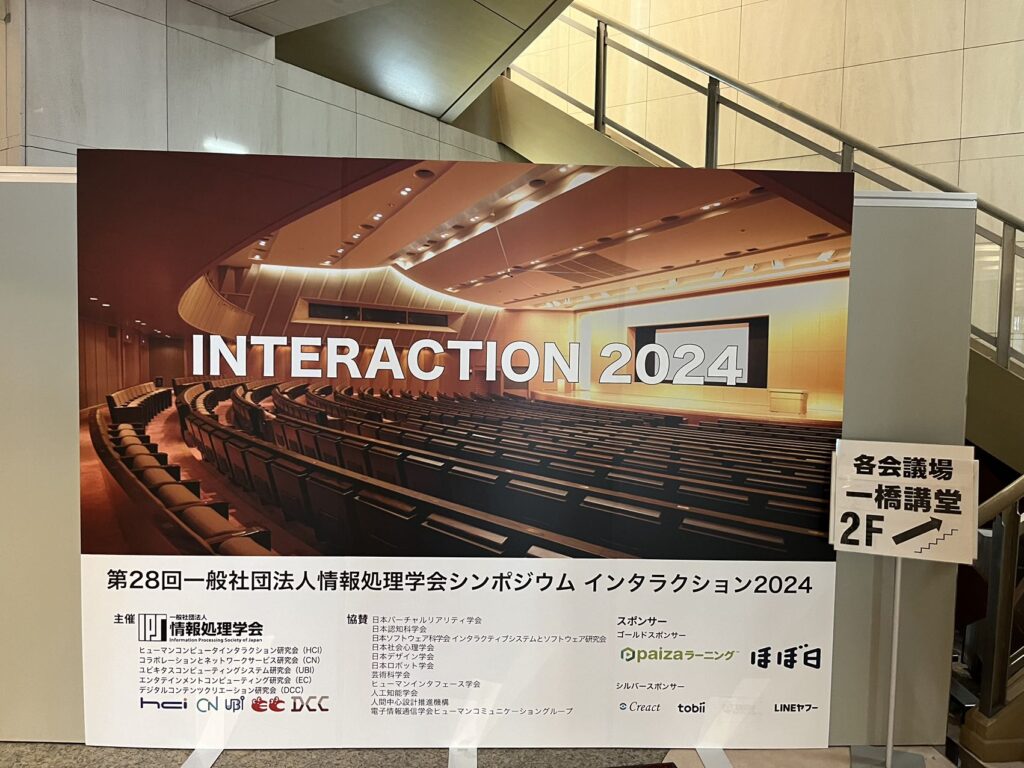
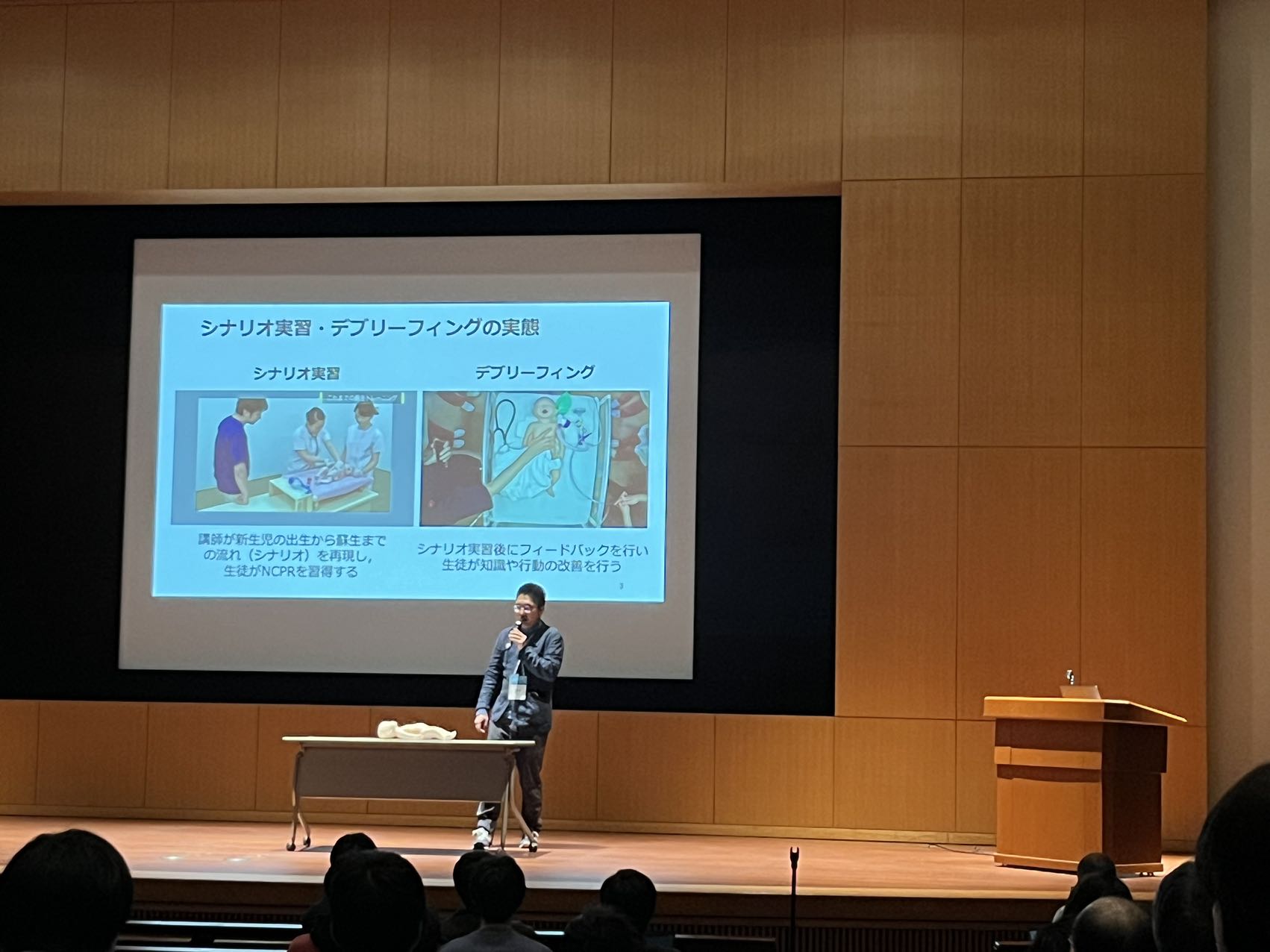
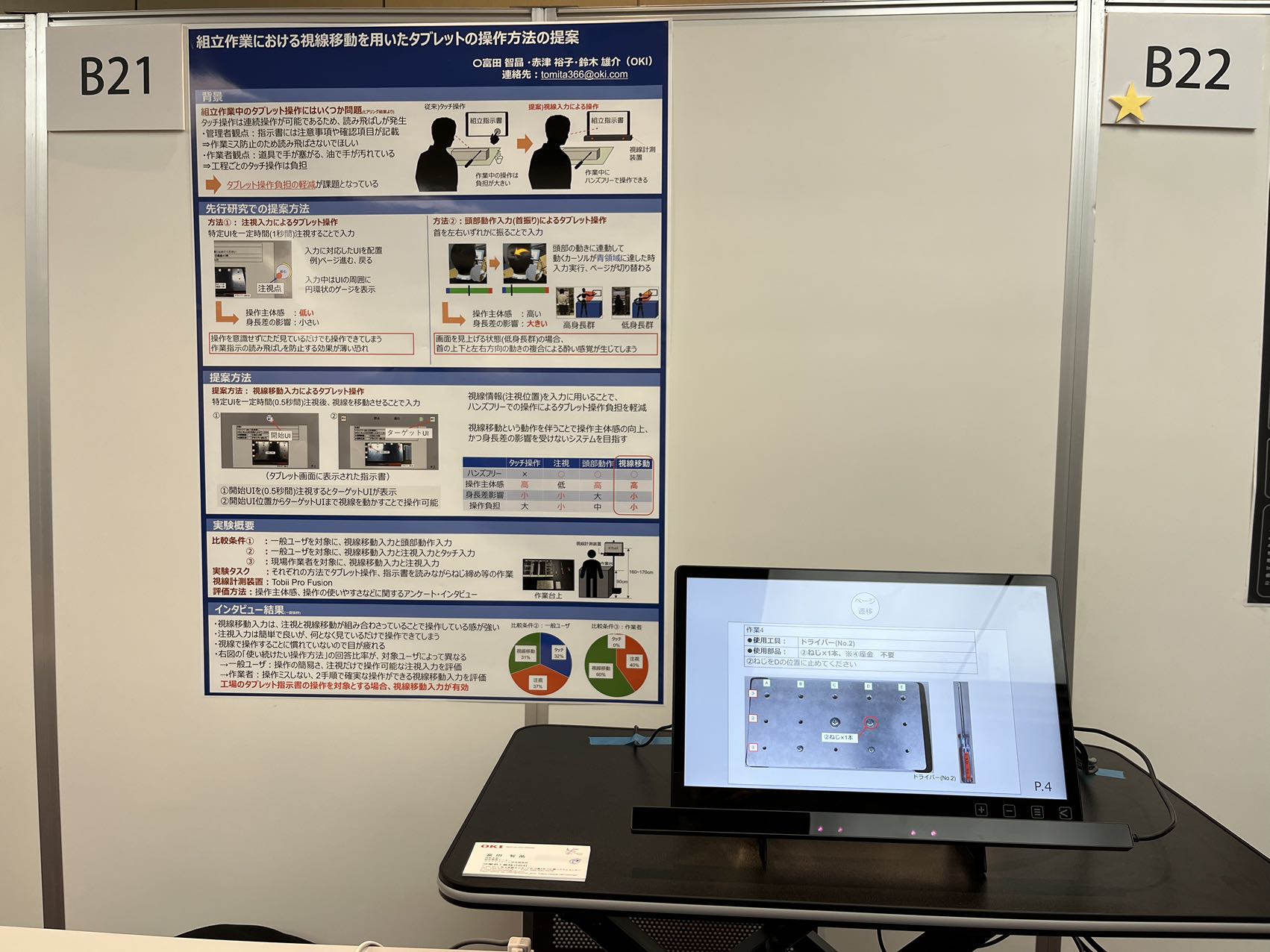
This system was developed by a company and uses gaze control to turn pages in assembly manuals, employing Tobii for eye tracking. Using it feels very effortless. They informed me that the system is currently in the experimental phase and hasn’t been officially deployed yet. Naturally, there are still some points that need improvement.
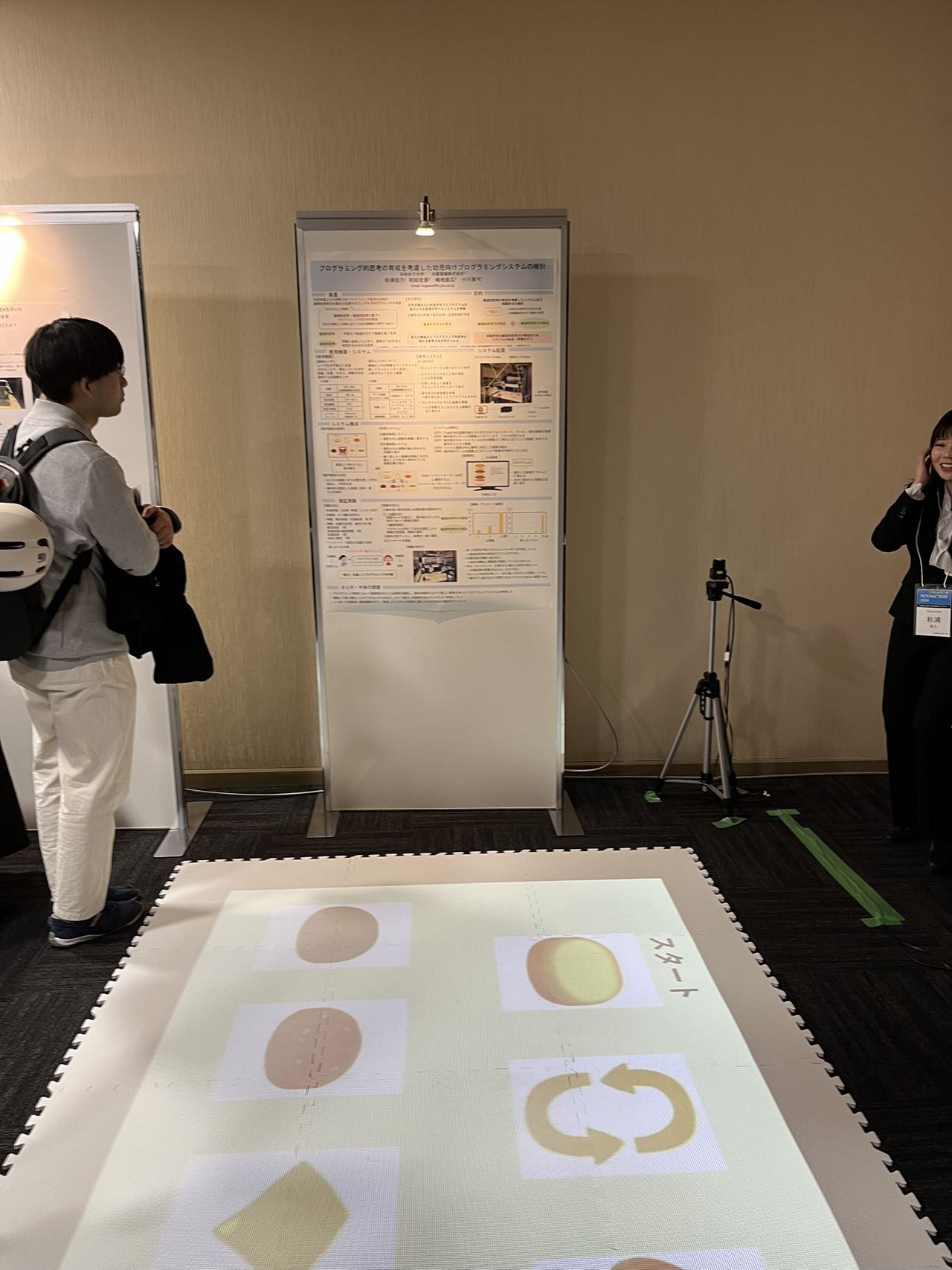
This system, aimed at young children, fosters programming thinking. Although it might seem like just playing simple games, I believe this system underscores the current emphasis on coding education. At Interaction 2024, I observed numerous studies related to support for coding education, which highlights the future importance of programming education.
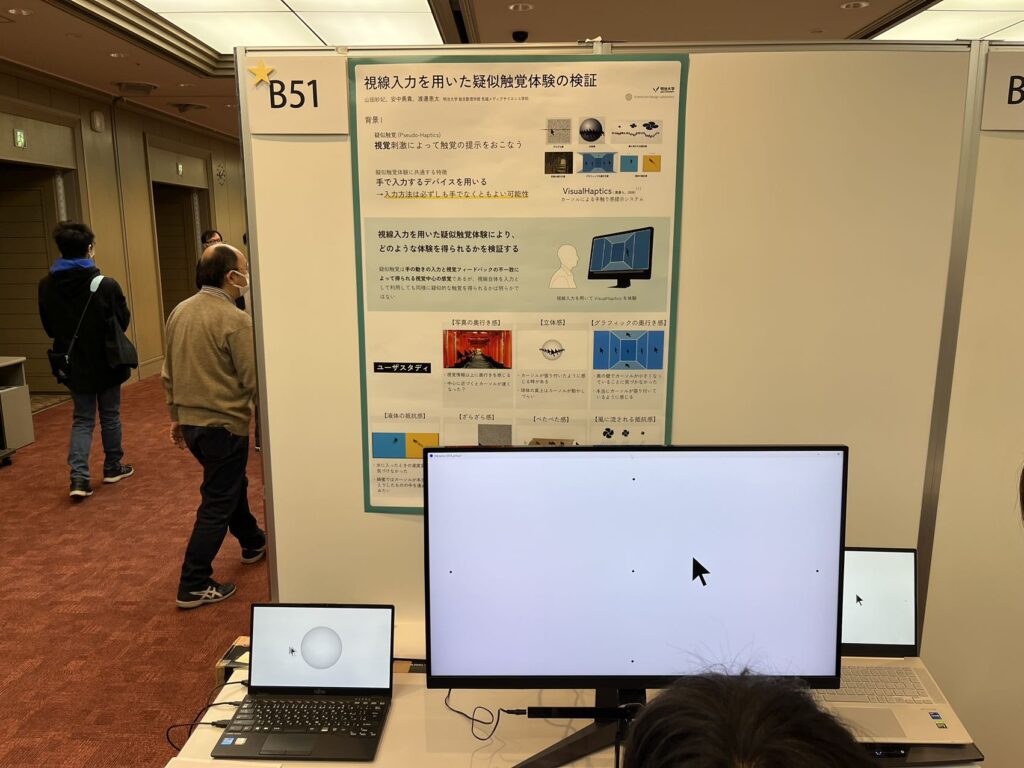
This study explores the concept of pseudo-haptics, where users can perceive tactile sensations without actual haptic feedback devices, simply by subtly altering the position and speed of a cursor. Related research includes “Visual Haptics,” which replicates the feeling of physically touching objects by manipulating cursor movement and deformation based on the state of the object being touched. This approach can simulate various sensations such as roughness, viscosity, three-dimensionality, depth, resistance in liquids, and resistance as if being blown by the wind. In this research, the cursor manipulation was achieved using eye-tracking technology provided by Tobii.
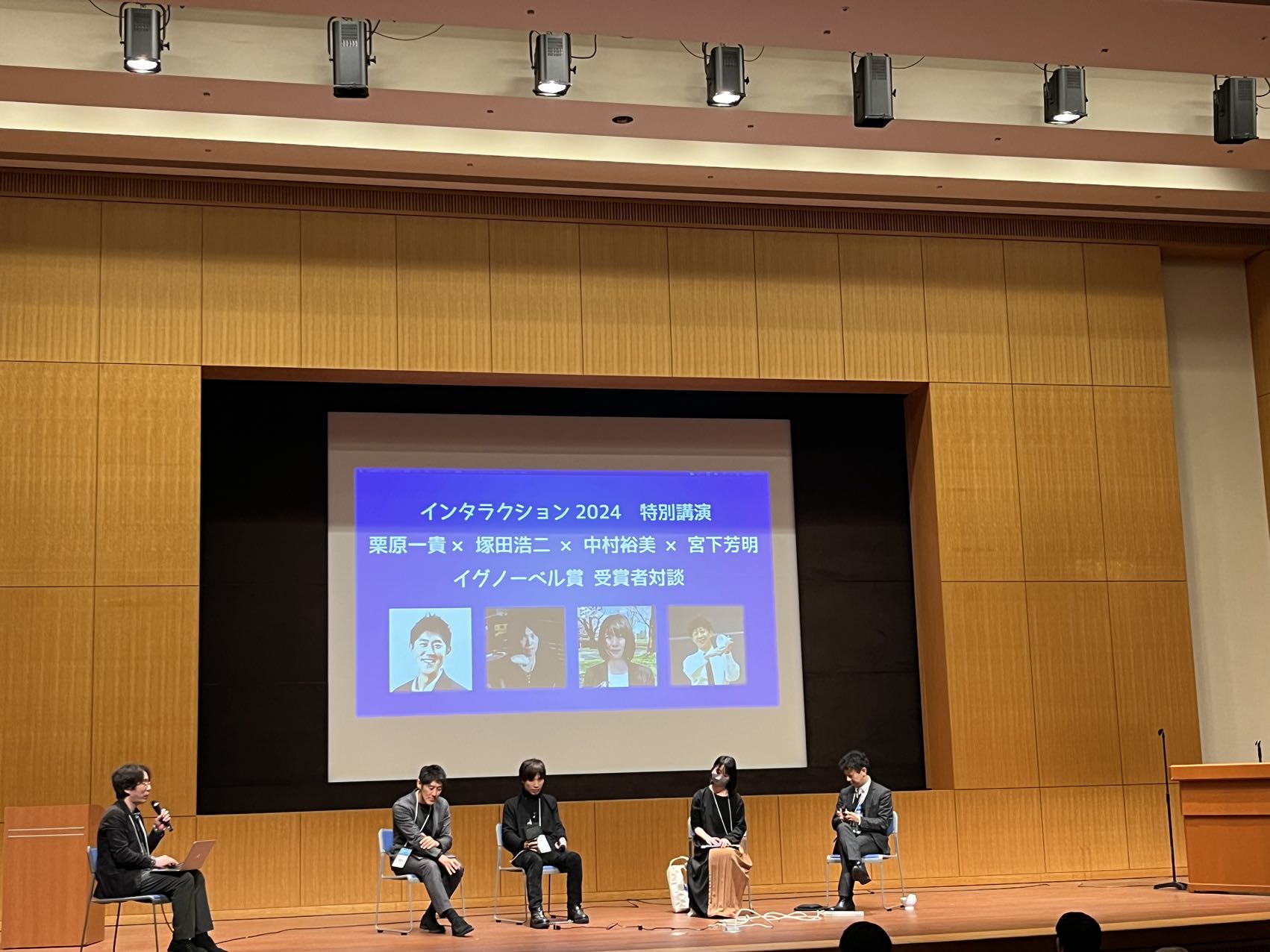
Several professors shared their award-winning experiences and research insights with the students, engaging in a fruitful exchange. There were also moments when students posed questions, to which the professors provided detailed responses. I found this lecture to be incredibly enriching.
As Interaction 2024 ends, I reflect on these past few days with a sense of profound gratitude and fulfillment. This conference has been an invaluable learning opportunity for me. Each lecture and demo experience have taught me so much. I believe the inspiration and knowledge gained at Interaction 2024 will greatly assist and enlighten me in my future studies and work endeavors. My heartfelt thanks go to Interaction 2024 for this unforgettable journey. I eagerly look forward to next encounter.